Understanding Lift Stations SCADA Alarms for Efficient Business Operations
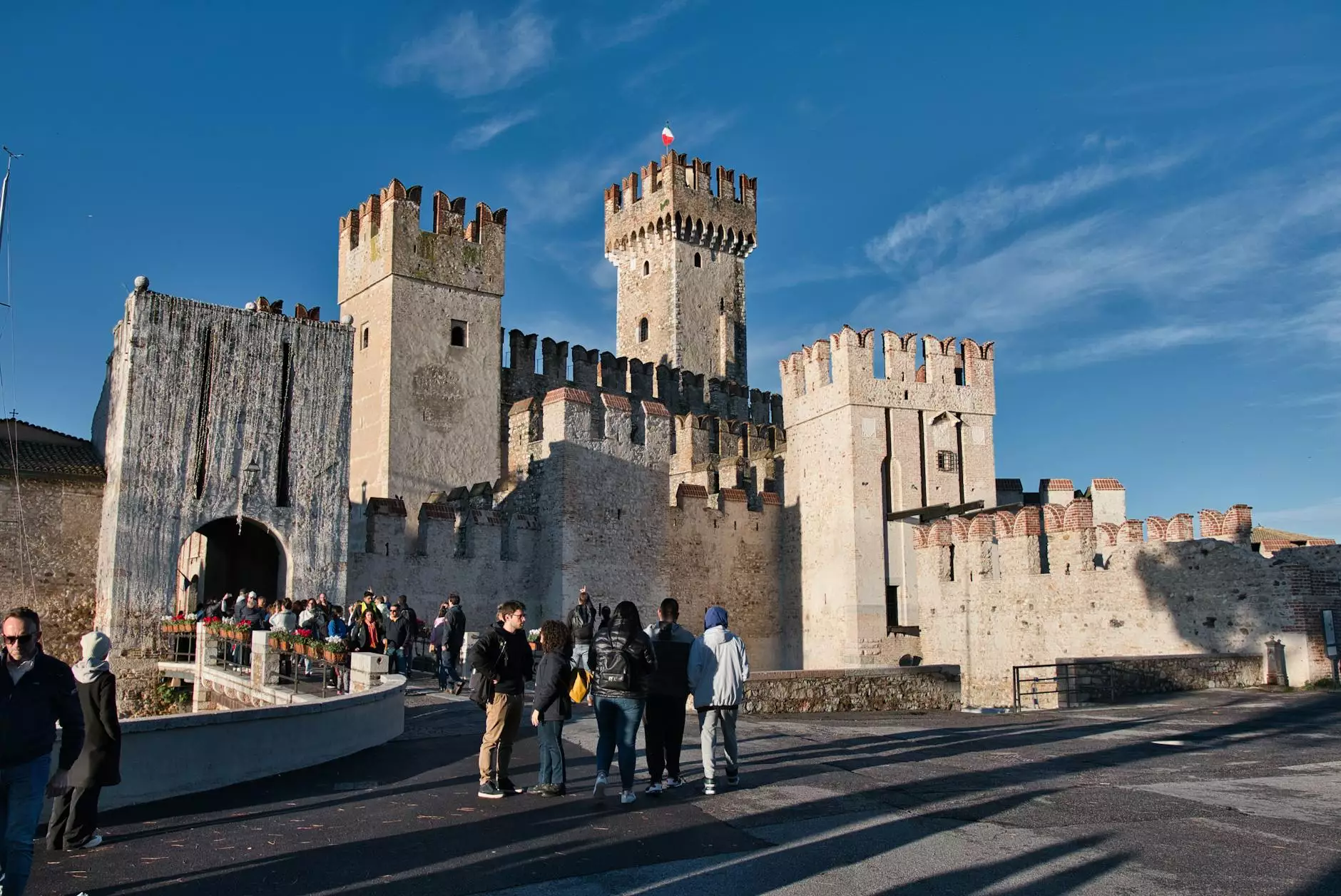
In the modern landscape of industrial operations, lift stations SCADA alarms play a crucial role in ensuring efficiency, safety, and operational continuity. Particularly for businesses in sectors such as Auto Parts & Supplies and Safety Equipment, understanding and implementing advanced monitoring systems is essential. This article delves into the depths of lift stations and their associated SCADA (Supervisory Control and Data Acquisition) systems, providing insights that can empower your business to enhance performance and safety.
What is a Lift Station?
A lift station, often referred to as a pump station, is a facility designed to move fluids (often wastewater) from lower to higher elevations. This is essential in areas where gravity alone cannot provide the necessary flow levels for effective wastewater management. Lift stations are equipped with various components, including:
- Pumps: These are the core components responsible for moving fluids.
- Valves: Used to control fluid flow and pressure.
- Piping: Connects various components and delivers fluids to their destination.
- Electrical systems: Power the pumps and control systems.
The Role of SCADA in Lift Stations
SCADA systems are vital for real-time monitoring and control of industrial operations. In the context of lift stations, SCADA provides:
- Real-Time Data Monitoring: Operators can view operational parameters such as pump status, fluid levels, and alarm conditions.
- Remote Control: Enables operators to manage operations from a distance, reducing the need for on-site personnel.
- Data Acquisition: Collects historical data for analysis and reporting, which is essential for operational improvement.
- Alarming and Notifications: Alerts operators to irregularities, such as pump failures or excessive fluid levels, ensuring rapid response times.
How Lift Stations SCADA Alarms Enhance Safety
One of the most significant benefits of implementing lift stations SCADA alarms is the enhancement of safety protocols. Here’s how:
- Early Detection of Failures: SCADA systems can monitor pump performance and detect anomalies early. This allows for preventative maintenance, reducing the risk of operational failures.
- Emergency Notifications: In the event of a malfunction, SCADA systems trigger alarms, notifying personnel to take immediate action, which is crucial for preventing spills or safety hazards.
- Compliance with Safety Regulations: Many industries have stringent regulations regarding wastewater management. SCADA systems help ensure compliance, reducing legal risks and enhancing public safety.
- Data Logging for Safety Audits: Historical data collected by SCADA systems can be vital during safety audits, showcasing compliance and operational integrity.
The Impact on Operational Efficiency
Beyond safety, lift stations SCADA alarms significantly influence operational efficiency in various ways:
- Optimized Resource Utilization: By providing insights into equipment performance, operators can make informed decisions about resource allocation and maintenance scheduling.
- Reduced Downtime: With proactive monitoring and alarms, systems can be maintained before failures occur, resulting in less downtime and more consistent operations.
- Improved Decision-Making: Access to real-time data allows for better decision-making regarding operations, enhancing overall performance.
- Cost Savings: By preventing major failures and optimizing operations, businesses can save significantly on maintenance costs and operational expenditures.
Implementing SCADA in Lift Stations
Implementing a SCADA system in lift stations involves several critical steps. Here’s a comprehensive guide:
1. Assessment of Needs
Begin with a thorough assessment of your operations and identify the specific needs that a SCADA system will address in your lift stations. Consider factors such as:
- Current operational challenges
- Regulatory requirements
- Desired level of automation
- Budget constraints
2. Choosing the Right SCADA System
Select a SCADA system that aligns with the operational needs identified in the assessment. Consider features like:
- User interface suitability
- Data integration capabilities
- Scalability for future needs
- Support and maintenance offered by the vendor
3. Installation and Integration
Work with experts to install the SCADA system and integrate it with existing equipment. This process may involve:
- Electrical and networking installations
- Connection of sensors and alarms
- Configuration of software settings
4. Training Personnel
Ensure your team is adequately trained on using the SCADA system. Comprehensive training should cover:
- Operational procedures
- Reaction protocols during alarms
- Data interpretation and usage for decision making
5. Regular Maintenance and Updates
Establish a schedule for regular maintenance and updates of both hardware and software components of the SCADA system. This will ensure continued reliability and performance.
Conclusion
The integration of lift stations SCADA alarms into business operations is not just a technological upgrade; it is a vital step toward enhancing both safety and efficiency. For companies in sectors like Auto Parts & Supplies and Safety Equipment, investing in SCADA systems can lead to significant operational improvements. By ensuring that your lift stations are equipped with advanced monitoring and alarm systems, you prepare your business not only to meet regulatory compliance and safety standards but also to achieve greater efficiency and cost-effectiveness.
As industries evolve, staying ahead with innovative solutions such as SCADA will differentiate your business in the competitive market. Embrace the future of operational excellence today by investing in lift stations SCADA alarms and proactively managing the critical systems that keep your operations running smoothly.