The Ultimate Guide to Plastic Injection Molding Manufacturers
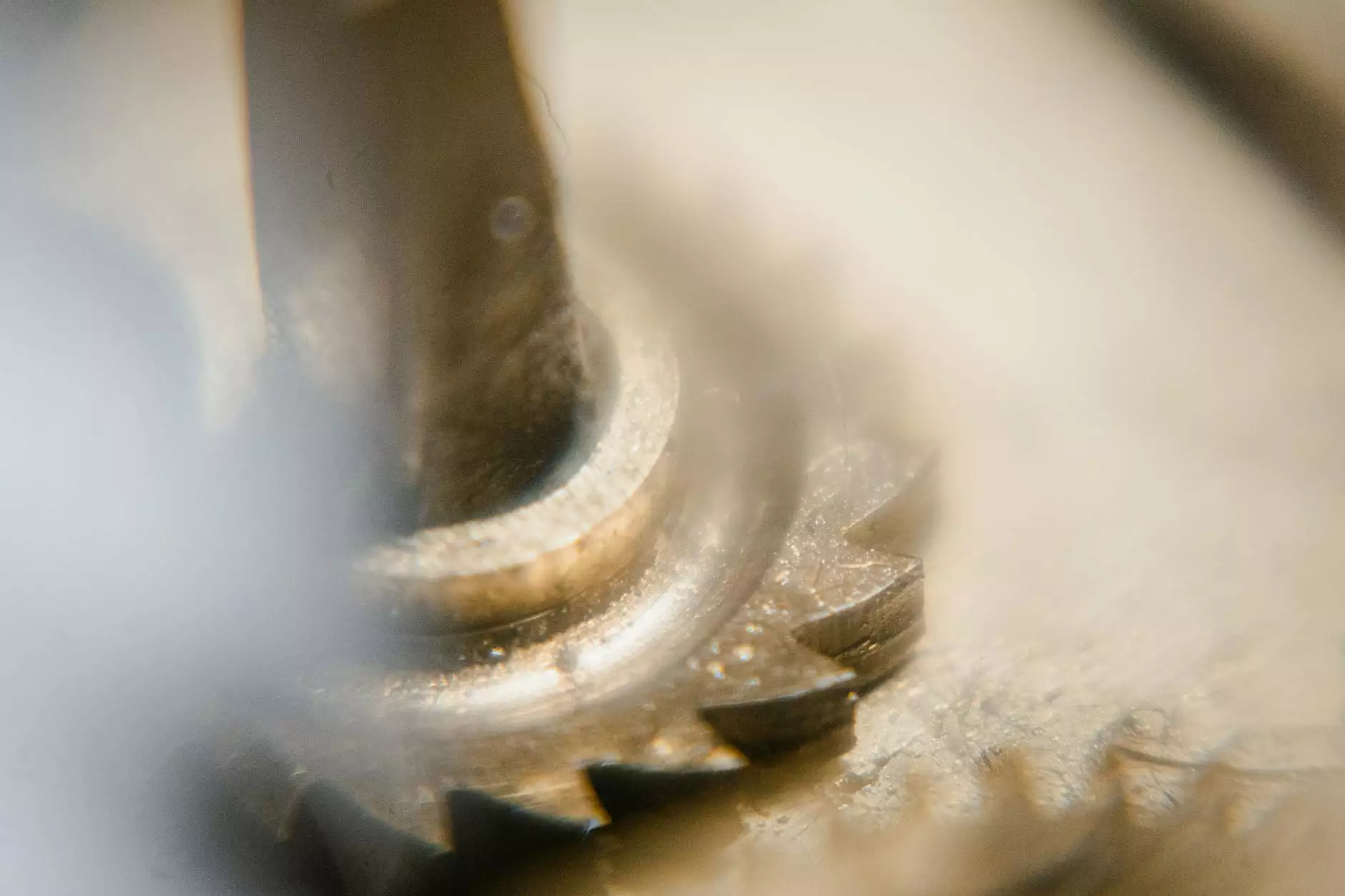
In the dynamic realm of manufacturing, plastic injection molding stands out as one of the most efficient and versatile methods of producing plastic components. As a plastic injection molding manufacturer, understanding the intricacies of this process is fundamental to delivering high-quality products to meet diverse market needs. In this comprehensive guide, we will delve into the world of plastic injection molding, illuminating its processes, applications, advantages, and the role of manufacturers in this sector.
Understanding Plastic Injection Molding
Plastic injection molding is a manufacturing process used to create parts by injecting molten material into a mold. This method is fundamental in producing a wide array of products, from everyday items to complex components used in various industries. The injected materials are typically thermoplastics or thermosetting plastics, selected based on the desired properties of the end product.
The Injection Molding Process
The process of plastic injection molding consists of several critical steps:
- Material Preparation: The chosen plastic resin is dried to remove any moisture, ensuring optimal flow and consistency during molding.
- Injection: The dry resin is heated to a molten state and injected under high pressure into a precisely designed mold.
- Cooling: The molten plastic cools and solidifies within the mold, taking the shape of the desired product.
- Mold Opening: Once cooled, the mold opens, and the newly formed part is ejected.
- Finishing: The molded component may require additional processes such as trimming, painting, or assembly to achieve the final product.
Benefits of Plastic Injection Molding
The choice of plastic injection molding offers numerous advantages for manufacturers, businesses, and consumers alike:
- High Efficiency: This process allows for mass production, drastically reducing manufacturing time and costs.
- Consistency: Each part produced is uniform, minimizing variations and ensuring quality control.
- Complex Geometries: Injection molding allows manufacturers to create intricate designs that would be challenging to achieve with other methods.
- Material Versatility: A wide variety of plastic resins can be used, offering options for different physical and chemical properties.
- Reduced Waste: The process generates minimal waste compared to traditional machining techniques, making it a more sustainable option.
The Role of Plastic Injection Molding Manufacturers
Plastic injection molding manufacturers serve as the backbone of the industry, transforming resin materials into finished products. Their expertise and capabilities include:
Design and Engineering
Manufacturers often start the process with extensive design work. This involves:
- Collaborating with clients to fully understand product specifications and requirements.
- Utilizing CAD software for designing parts and molds, which optimizes the production process.
- Conducting feasibility studies to confirm that the desired designs can be effectively produced.
Prototyping
Before mass production, plastic injection molding manufacturers often create prototypes. This step is essential for:
- Testing the design for functionality and aesthetics.
- Making necessary adjustments to the mold before scaling production.
- Providing a tangible model for client approval.
Production and Quality Assurance
During the production phase, manufacturers maintain rigorous quality assurance processes, which include:
- Monitoring injection parameters like temperature and pressure to ensure consistency.
- Regular testing of samples to ensure they meet predefined standards.
- Utilizing advanced technology such as robotics for more accurate and efficient production.
Post-Production Services
The role of a plastic injection molding manufacturer extends beyond initial production. They often provide:
- Secondary operations such as assembly, painting, and packaging.
- Logistics support to ensure timely delivery of the final products to clients.
- Customer service for ongoing support and addressing any issues that may arise.
The Future of Plastic Injection Molding
The manufacturing landscape is constantly evolving, and the future of plastic injection molding is no exception. Several trends are shaping its development:
Technological Advancements
As technology progresses, manufacturers are adopting more sophisticated machinery and software:
- Industry 4.0: Integration of smart manufacturing technologies, including IoT, to monitor processes and optimize production in real time.
- 3D Printing: Complementing traditional molding techniques with additive manufacturing for rapid prototyping and limited-run production.
- Advanced Materials: Developing bio-based and recyclable plastics to meet increasing environmental concerns.
Sustainability Initiatives
With growing emphasis on environmental impact, plastic injection molding manufacturers are focusing on sustainability:
- Adopting practices that reduce energy consumption and waste.
- Implementing closed-loop recycling systems for plastic materials.
- Pursuing certifications and compliance with environmental regulations to enhance corporate responsibility.